Essential Signs for Motor Repair Assistance in Columbus
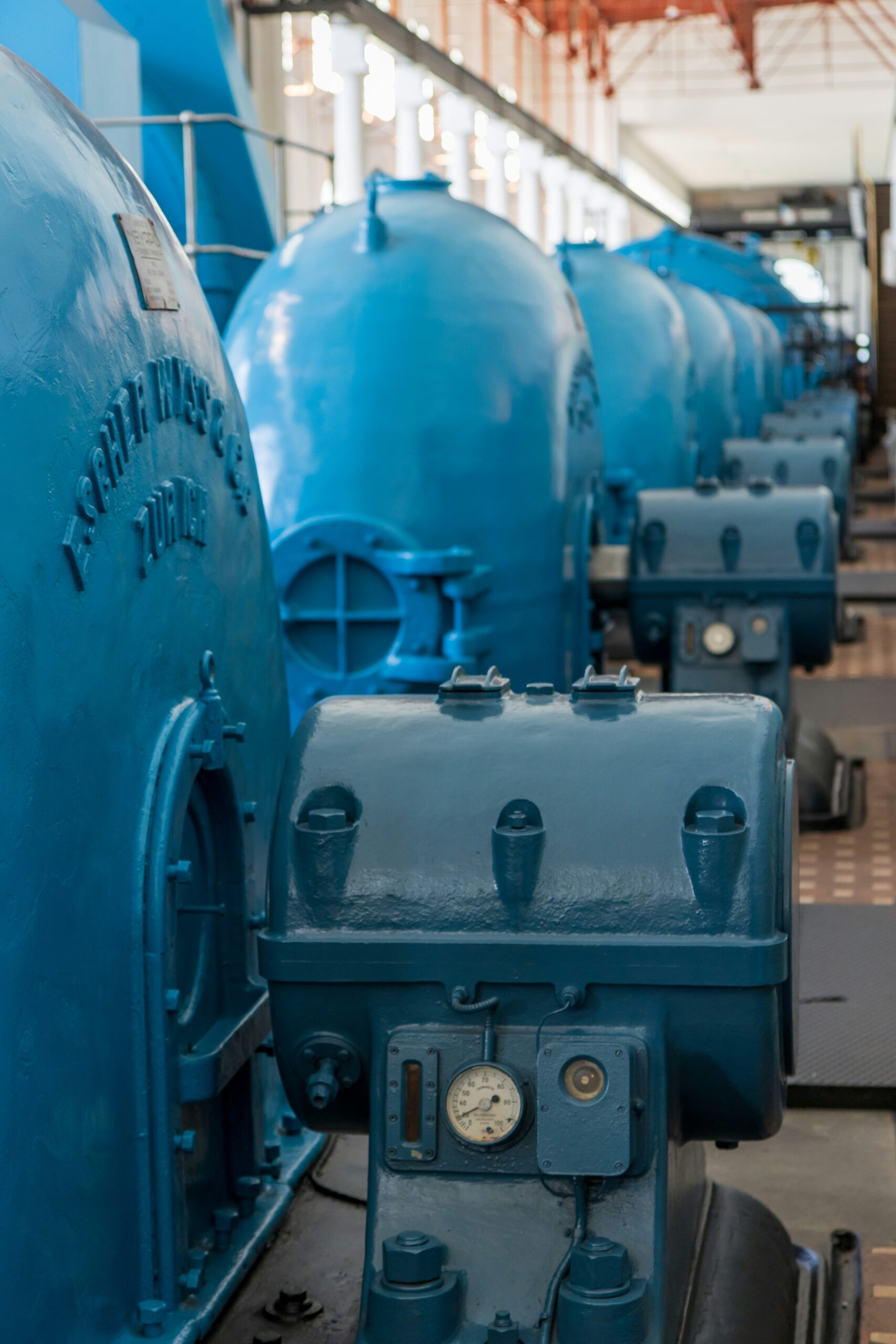
hen to Call for Emergency Industrial Motor Repair in Columbus
Emergency industrial motor failure can halt operations, leading to costly downtime. Knowing when to seek immediate repair is crucial. This article will cover key signs of motor problems, the risks of delaying repairs, and how to choose the right service in Columbus. By understanding these points, readers can minimize downtime and make informed decisions regarding their industrial motors. Identifying issues early can save time and resources, ensuring operations run smoothly.
Key Takeaways
- Unusual noises often indicate mechanical issues requiring immediate professional attention
- Regular inspections can prevent costly repairs and maintain operational efficiency in industrial settings
- Delaying motor repairs can lead to significant downtime and increased operational costs
- Understanding the urgency for repairs is crucial for keeping essential operations running smoothly
- Investing in quality motors enhances performance and reduces the likelihood of urgent repair needs
Identifying Signs of Motor Failure Needing Immediate Attention

Unusual noises such as grinding or buzzing can signal mechanical issues, while a sudden loss of power or efficiency may indicate a need for repair. Frequent trips or overload problems suggest underlying faults, and visible damage or overheating on the motor warrants immediate action. Each of these signs helps professionals determine when to seek emergency industrial motor repair in Columbus.
Unusual Noises Indicating Mechanical Issues
Unusual noises from an industrial motor can be clear indicators of mechanical issues that require immediate attention. Grinding or buzzing sounds often signal potential internal damage or wear, which, if not addressed promptly, could lead to more significant repairs and downtime. A quick response from a professional is crucial for maintaining efficient operations and ensuring reliable customer service during emergencies.
- Grinding sounds suggest internal wear.
- Buzzing noises can indicate electrical problems.
- Ignoring these signals may lead to costly repairs and disruptions.
Sudden Loss of Power or Efficiency
A sudden loss of power or efficiency in an industrial motor can pose serious safety risks, especially in sectors such as construction where hoists are frequently used. This drop in performance may be attributed to worn bearings or other mechanical issues, jeopardizing not only equipment functionality but also the well-being of customers and employees. Immediate professional evaluation is essential to prevent further damage and ensure smooth operations at all times.
Frequent Trip or Overload Issues
Frequent trips or overload issues with an industrial motor can be critical signals indicating the need for immediate attention. Such problems often stem from wear and tear on machine tools or heavy equipment, leading to performance disruptions that can halt operations. Professionals in information technology or mechanical repair can quickly assess these issues, ensuring that necessary repairs are applied before they escalate into more severe complications, safeguarding both equipment and workforce safety.
Visible Damage or Overheating on the Motor
Visible damage or overheating on an industrial motor is a critical concern that demands immediate intervention. A technician can quickly identify signs of physical wear, such as cracks or discoloration, that indicate potential failure. Addressing these issues promptly not only prevents costly repairs but also promotes effective leadership in manufacturing environments, ensuring the safety of equipment and personnel.
Ignoring signs of motor failure can lead to bigger problems. Understanding the risks of waiting too long could save more than just time; it might save a costly breakdown.
Understanding the Risks of Delaying Motor Repairs

Delaying motor repairs can have significant consequences on production and lead to prolonged operational downtime. Increased repair costs can arise alongside the potential for more extensive damage, affecting machinery involved in sectors like nursing and aerospace. Furthermore, malfunctioning motors pose safety hazards that must be addressed immediately. Each of these risks highlights the necessity for timely intervention to ensure reliable performance and safety in industrial settings.
Impact on Production and Operational Downtime
Delaying motor repairs can significantly impact production and lead to operational downtime, especially in industries reliant on welding and metal fabrication. For businesses, any disruption to machinery can cause delays in essential services and affect the overall quality of care and education. Timely motor repair not only maintains motion within machines but also ensures consistent productivity, minimizing the risk of operational delays that could strain resources and customer trust.
Increased Repair Costs and Potential for Further Damage
Delaying repairs on industrial motors can significantly increase costs and lead to extensive damage. As issues escalate, the price for parts and labor can rise sharply, particularly if a qualified electrician is needed to handle the complexities of the situation. For example, a malfunctioning crane motor left unrepaired may not only cause immediate operational disruptions but also necessitate emergency service, resulting in further financial strain and operational setbacks.
Safety Hazards Associated With Malfunctioning Motors
Malfunctioning motors present significant safety hazards that can jeopardize both employees and operational efficiency. When motors fail, issues such as electrical shorts or overheating can lead to dangerous situations, including fires or equipment breakdowns. Engaging skilled technicians who specialize in automation and emergency response is essential for addressing these risks promptly, where industrial safety standards are strict. By prioritizing timely repairs through professional services like ierservices, businesses can safeguard their workforce and maintain safe operating environments.
When a motor shows signs of distress, understanding its needs becomes urgent. Next, key factors will reveal how to identify which repairs must be handled right away.
Key Factors in Determining Emergency Repair Needs
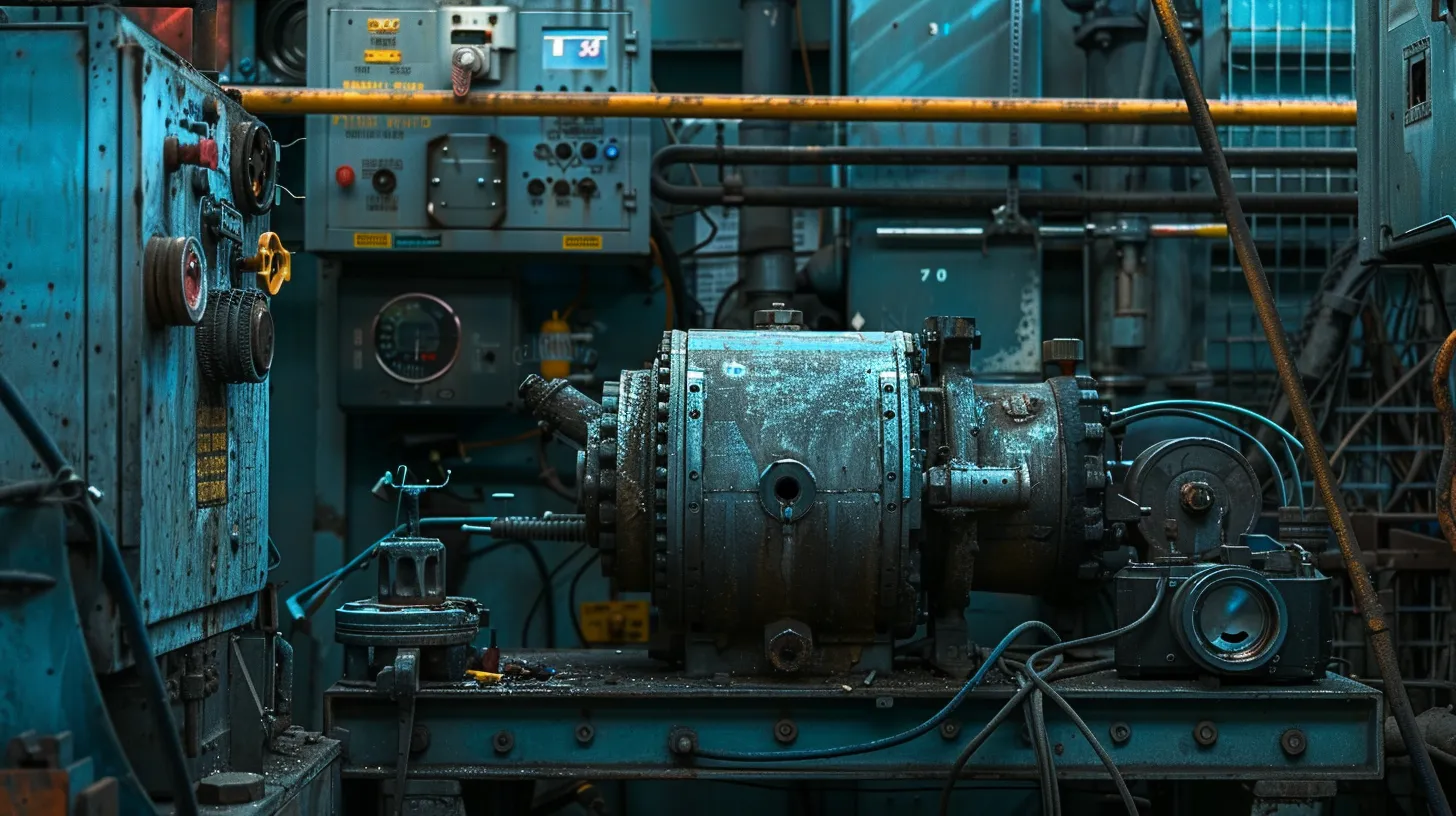
The type of operation and its vulnerabilities are significant when assessing the need for emergency industrial motor repair. The age and condition of the electric motor also play a crucial role in determining repair urgency. Furthermore, the frequency and nature of past repairs can indicate whether issues are becoming more severe. Each of these factors helps professionals decide when immediate attention is necessary to prevent costly downtime.
Type of Operation and Its Vulnerabilities
The type of operation significantly influences the urgency of calling for emergency industrial motor repair. For instance, industries like human resource management and criminal justice often rely on systems that require uninterrupted power, such as elevators. If these systems fail, it can disrupt critical services and safety protocols, emphasizing the necessity for swift intervention.
Age and Condition of the Industrial Motor
The age and condition of an industrial motor significantly impact its performance and the urgency of required repairs. Older motors may be more prone to mechanical issues, particularly if they have been in operation for extended periods without proper maintenance. For example, facilities utilizing diesel engines alongside robotics may find that outdated motors lead to increased energy costs and inefficiencies, necessitating immediate evaluation to avoid costly disruptions in production. Understanding these factors can guide operators in deciding when to seek emergency industrial motor repair in Columbus:
- Older motors may require more frequent repairs.
- Worn components can lead to system failures.
- Regular maintenance is essential to prolong motor life.
Frequency and Nature of Past Repairs
The frequency and nature of past repairs play a vital role in determining the urgency for emergency industrial motor repair in Columbus. A machine with a history of frequent breakdowns or repairs might signal deeper underlying issues, particularly in sectors like culinary arts or electronics where operational reliability is crucial. For instance, a kitchen appliance that frequently malfunctions can disrupt food preparation, negatively impacting service inventory and overall productivity, underscoring the need for timely intervention to avoid more extensive problems.
When a crisis strikes, knowing what to look for becomes vital. The next steps will guide you through immediate actions needed for emergency repairs.
Steps to Take When Emergency Repairs Are Needed
Assessing the situation is the first step when emergency industrial motor repair is needed. Professionals should identify symptoms like unusual noise or loss of power. Next, contacting emergency repair services with specific details helps ensure a swift response. Finally, documenting the problem thoroughly aids service technicians in addressing issues with the fleet, ensuring minimal disruption to the workforce and operations.
Immediately Assess the Situation and Identify Symptoms
Immediately assessing the situation is vital when facing industrial motor issues in logistics. Professionals should carefully listen for unusual sounds stemming from the engine or note any irregularities in performance that could indicate problems with the chassis or other components. Identifying these symptoms quickly allows for efficient troubleshooting and helps safeguard the warranty of the equipment by ensuring timely repairs:
Contact Emergency Repair Services With Specific Issues
When an industrial motor requires immediate attention, contacting emergency repair services with specific details is vital for a swift resolution. Providing clear information about the observable issues, such as unusual noises or power loss, allows technicians to prepare effectively before arriving on site. This proactive approach fosters quicker diagnostics and enhances the overall repair process, minimizing downtime and disruption to production.
Document the Problem for Service Technicians
Documenting the problem for service technicians is a critical step in the emergency repair process for industrial motors. Clear records of symptoms, such as unusual noises or power loss, enable technicians to quickly identify potential issues when they arrive on site. This proactive approach not only streamlines the repair process but also minimizes downtime, ensuring that businesses in Columbus can return to normal operations as swiftly as possible.
Emergency repairs can be a burden, but finding the right service is pivotal. In the following section, the focus shifts to choosing an industrial motor repair service that meets your needs effectively.
Choosing the Right Emergency Industrial Motor Repair Service
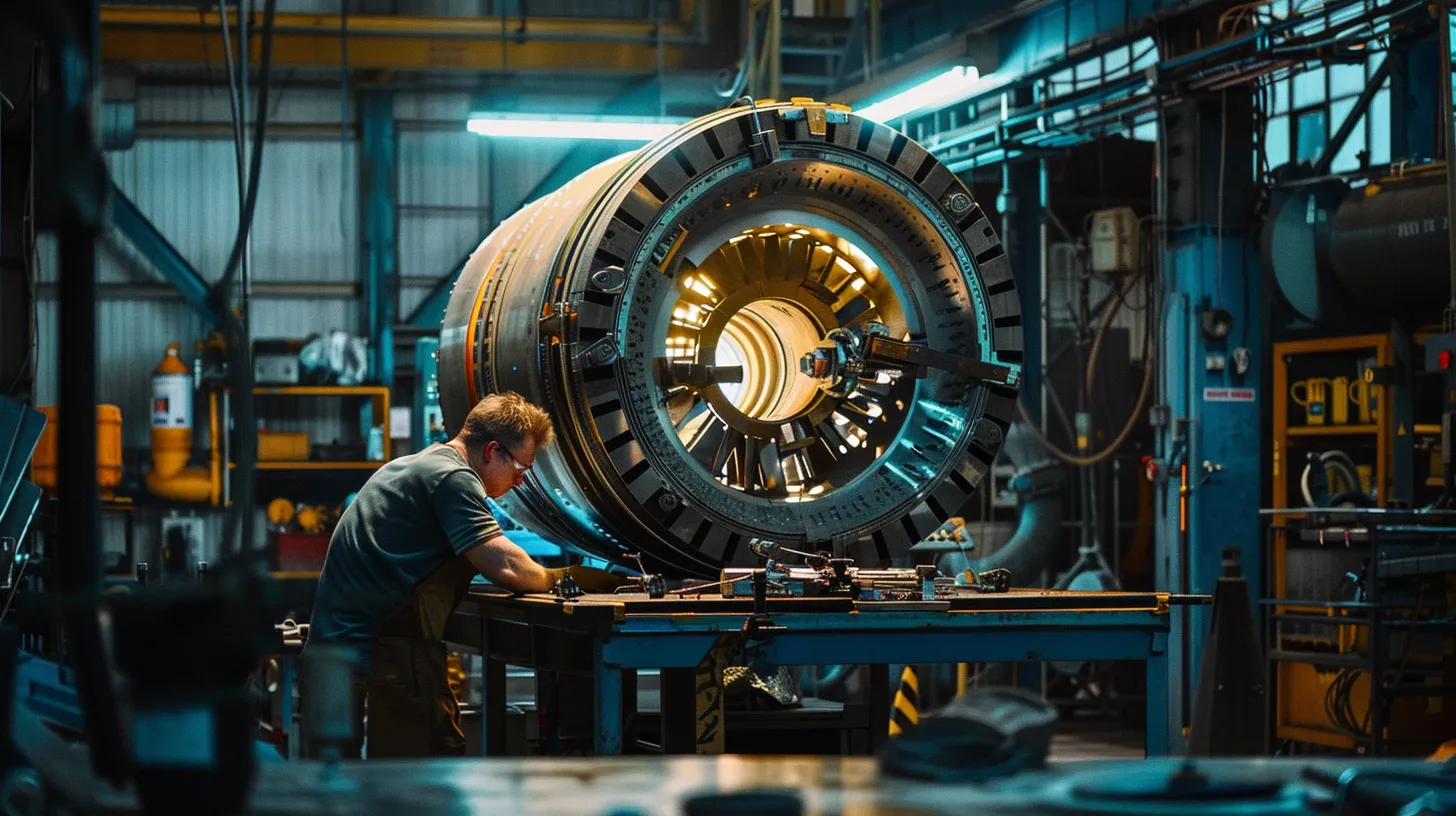
Choosing the right emergency industrial motor repair service in Columbus involves careful evaluation of several key factors. First, examining the qualifications and certifications of service providers is essential for ensuring expertise. Understanding their response times and availability helps in assessing how quickly assistance can be obtained. Lastly, reviewing customer feedback and case studies provides insight into their reliability and effectiveness. Each of these aspects is crucial for making an informed decision when urgent repairs are needed.
Evaluating Qualifications and Certifications of Service Providers
When selecting an emergency industrial motor repair service in Columbus, evaluating the qualifications and certifications of potential providers is essential. Professionals should look for technicians who hold industry-recognized credentials, as this indicates a solid foundation of knowledge and expertise in handling various motor issues. For instance, certifications from organizations like the National Institute for Certification in Engineering Technologies (NICET) demonstrate an adherence to standards that can ensure quality repairs and minimize downtime, ultimately protecting the investment in machinery.
Understanding Response Times and Availability
When selecting an emergency industrial motor repair service in Columbus, understanding response times and availability is critical for minimizing downtime. Businesses should inquire about how quickly technicians can respond to service calls, as delays can exacerbate equipment issues and disrupt operations. For example, a workshop needing immediate motor repairs could experience significant losses if the service provider cannot arrive promptly to address the malfunction.
Reviewing Customer Feedback and Case Studies
Reviewing customer feedback and case studies is essential when selecting an emergency industrial motor repair service in Columbus. Insights from previous clients can reveal the reliability and efficiency of a service provider, highlighting their ability to handle urgent repairs effectively. For instance, testimonials that discuss prompt response times and quality workmanship can guide businesses in making informed decisions, reducing the risk of prolonged downtimes and ensuring continuous operational productivity.
After selecting a reliable emergency motor repair service, the focus shifts to prevention. Understanding how to minimize the need for such urgent fixes leads to smoother operations and less stress for all involved.
Preventative Measures to Reduce Emergency Repair Needs
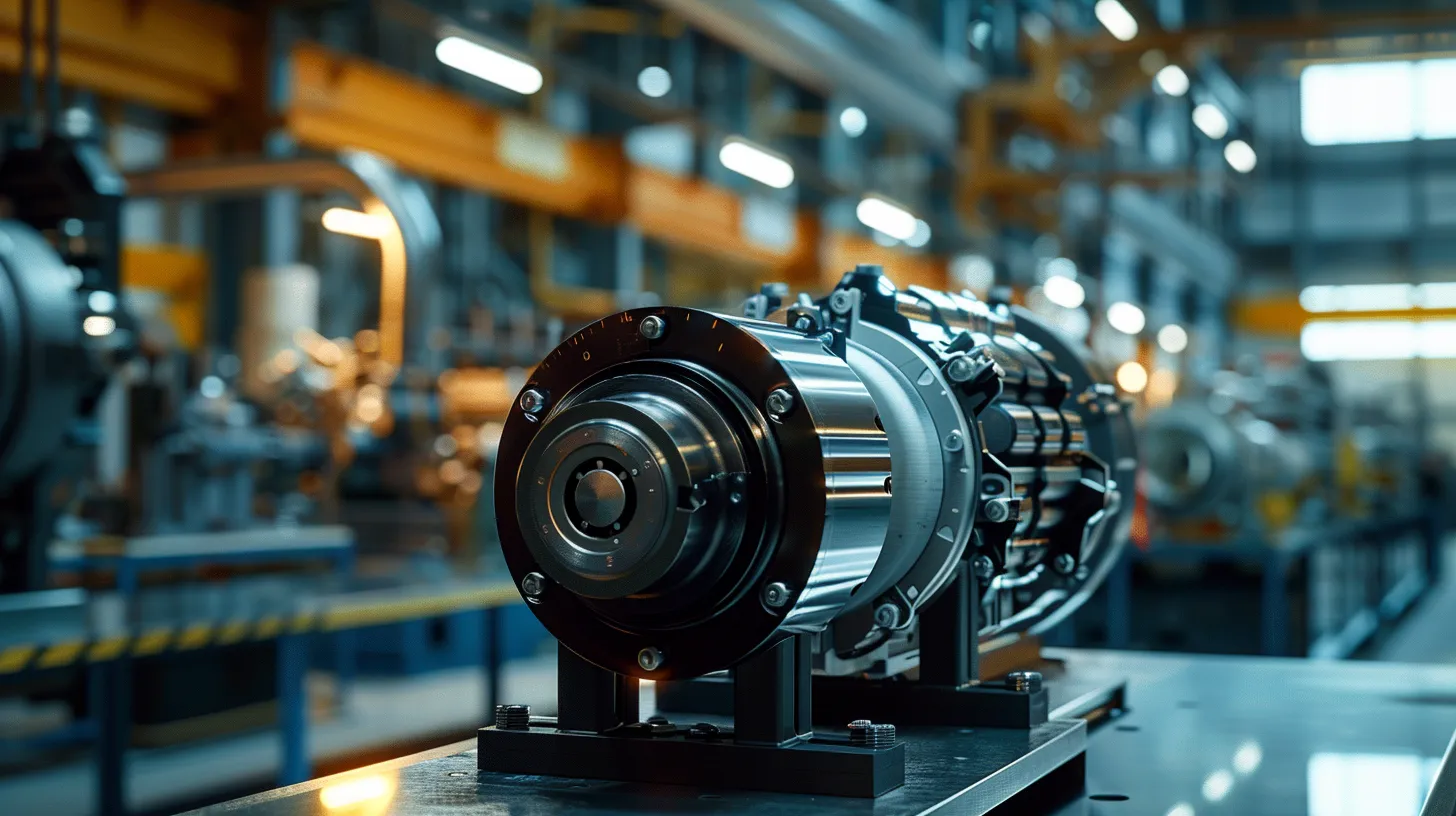
Conducting regular maintenance and inspections of industrial motors is crucial for identifying potential issues early. Investing in quality motors further enhances reliability and performance. Additionally, training staff on early detection of problems enables prompt reporting and action. These preventative measures significantly reduce the need for emergency industrial motor repair in Columbus, ensuring smoother operations and safeguarding productivity.
Conducting Regular Maintenance and Inspections
Conducting regular maintenance and inspections of industrial motors plays a pivotal role in preventing unexpected failures and ensuring consistent operational efficiency. By scheduling routine checks, businesses can identify potential issues before they escalate into costly repairs or prolonged downtimes. For example, regular lubrication of moving parts can help maintain performance and extend the lifespan of the motor, making it a vital practice for operators in Columbus who rely on these machines for productivity:
- Schedule routine inspections to catch wear and tear early.
- Implement a preventive maintenance plan tailored for specific motor types.
- Educate staff on how to identify early signs of motor issues.
Investing in Quality Industrial Motors
Investing in quality industrial motors is a proactive strategy that enhances operational reliability and reduces the likelihood of emergencies needing urgent repair in Columbus. High-quality motors typically offer better efficiency, longevity, and performance, helping to minimize breakdowns and associated costs. For example, facilities that choose reliable brands often experience fewer disruptions and can maintain consistent output, protecting both productivity and revenue over time.
Training Staff on Early Detection of Issues
Training staff on early detection of issues is a pivotal preventative measure to reduce the likelihood of emergency industrial motor repair in Columbus. By equipping employees with knowledge about common motor symptoms—such as unusual sounds or performance drops—organizations can enable quicker responses to potential problems. This proactive approach not only minimizes downtime but also enhances overall operational efficiency, ultimately safeguarding productivity in industrial environments:
- Educate staff on identifying unusual noises and power inefficiencies.
- Implement regular training sessions to refresh skills and knowledge.
- Encourage prompt reporting of any irregularities observed during operations.
Conclusion
Recognizing when to call for emergency industrial motor repair in Columbus is essential for maintaining operational efficiency and safety. Timely intervention can prevent costly downtimes, extensive repairs, and potential hazards that could jeopardize employee well-being. Regular maintenance and early detection of issues not only safeguard equipment but also ensure consistent productivity across various industries. Businesses must prioritize awareness of warning signs to take swift action, preserving resources and enhancing overall performance.