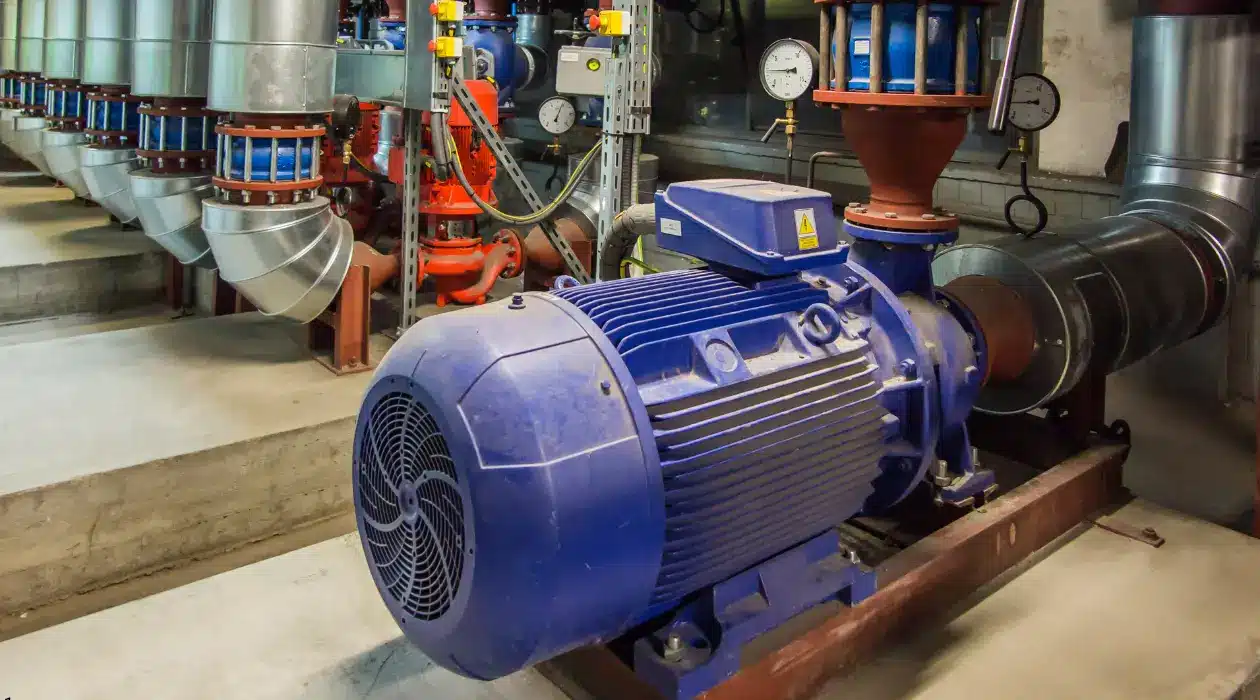
Top 7 Warning Signs Your Industrial Equipment Needs Emergency Repairs
Top 7 Warning Signs Your Industrial Equipment Needs Emergency Repairs Running a manufacturing plant or facility means relying on heavy-duty machinery, industrial motors, industrial pumps,